Final Report
Final Report
Community Healthcare is a medical office facility under construction in the Mid-Atlantic region. The design intent is to create a three story healthcare project to extend the network of care to the local community. The goal is to create a space where the specialists come to the patients and not the other way around. The primary tenant of this facility has a long standing history of providing exceptional healthcare to this community and has teamed up with Frauenshuh HealthCare Real Estate Solutions, one of the leading developers of medical office and ambulatory care facilities, to create this building.
The flat site in this suburban neighborhood drew attention from other corporations interested in developing the site as well. Fortunately, the primary tenant of this facility was warmly welcomed by the community and is expected to complete construction in January 2016, just 15 months after the issuance of the notice to proceed.
Frauenshuh brought Perkins +Will on as the architect of record and DPR Construction as the construction manager. This project was split into the core and shell (C&S) as one GMP package and the tenant interiors (TI) as another, of which both have the same project partners. While Frauenshuh holds both the C&S and TI contracts through their LLC, Frauenshuh is most interested in the C&S and the primary tenant in the TI. This medical office building is set to open in the spring of 2016.
The Community Healthcare building is located in the Mid-Atlantic region of the country with the intent to bring high quality medical care to local community. This three story medial office facility is being built out for a primary tenant occupying the first level and part of the second and third. The remaining spaces will be finished at a later date by other tenants. This report looked into altering four areas of the project in the hope of providing valuable alternative construction means and methods for future projects. Three of these analyses focused on issues or opportunities that could have improved constructability, accelerated the schedule, or reduced costs. The final analysis researched the critical industry topic of virtual mockups.
Analysis I | Precast Footings
The project experience approximately a five month schedule delay due to litigation, which was further delayed by weather delays pertaining to cold weather concrete. The foundations and structure all had to be completed during the winter months versus the initially planned summer installation. By using precast footings instead of the traditional cast-in-place method, this analysis found that the construction schedule could be accelerated, but the additional cost made this analysis not recommended.
Analysis II | Prefabricate the Building Envelope
With a tight schedule, the project is using temporary enclosure methods to maintain their interiors schedule. This analysis looked at prefabricating the exterior metal framing, sheathing, and insulation into panels in the effort to accelerate building dry-in. This alternative method of panelizing the exterior enclosure is recommended since it was found to minimize risk in damages and record incidents.
Analysis III | Masonry LINAC Vault
The linear accelerator (LINAC) vault was added to the core and shell GMP package fairly late in during design by the primary tenant. The system is a traditional LINAC vault assembly comprised of standard reinforced concrete system. The healthcare industry has been moving away from this system so this analysis looked at the benefits of using a masonry vault instead. However, it was found that the masonry LINAC vault only provided space savings through thinner walls for the same shielding capabilities. Therefore, a LINAC vault is not recommended for this project in its current location, since the vault is not limited by wall thickness or ceiling height, making the current concrete system the cheapest and simplest construction method for a LINAC vault.
Analysis IV | Virtual Mockups
In order to keep cost down, this project chose not to use BIM technologies to coordinate any building systems. Despite these decisions, this project has experienced its fair share of change orders due to constructability issues and late design changes. This analysis looked at potentially using virtual mockup technologies to mitigate change orders of these themes. Research was conducted for virtual mockup usage amongst leading companies in the industry. This research concluded that virtual mockup technologies are being used to identify and solve issues including constructability issues and design review. Therefore, implementing virtual mockups for this project and similar projects are highly recommended for their potential to save projects money.
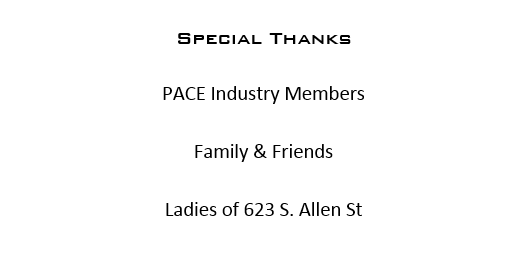
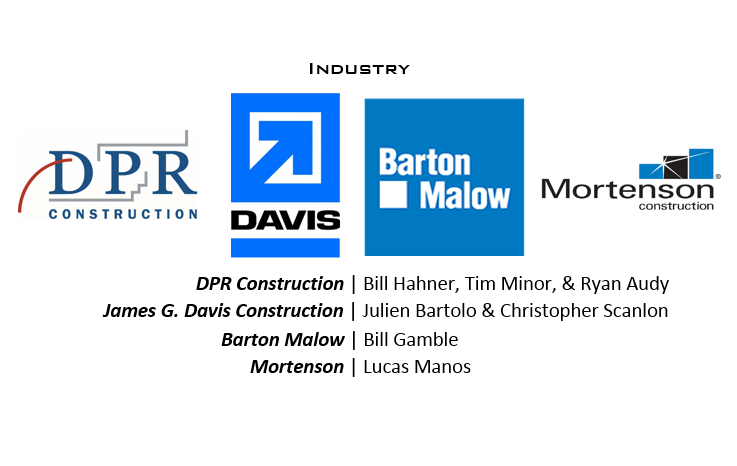

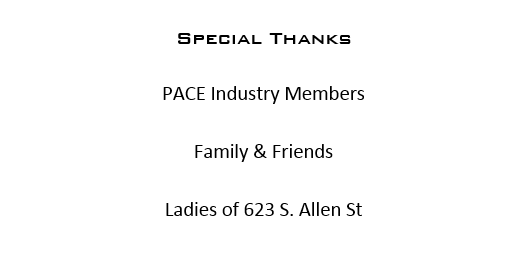