Building Statistics Part I
General Information
Building Name
Location and site
Building Occupant Name
Occupancy or function types
Size
Number of Stories above Grade
Dates of Construction
Actual Cost Information
Project Delivery Method
*Note: Information may have been altered at the request of the Owner.
Community Healthcare*
Mid-Atlantic Region
Undisclosed
Medical Office
108,000 GSQFT
3 Levels
Sept. 2014 to Jan. 2016
Undisclosed
Construction Manager at Risk
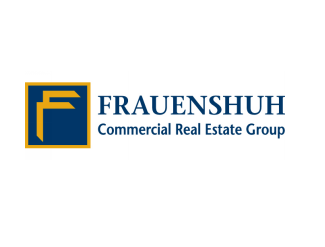



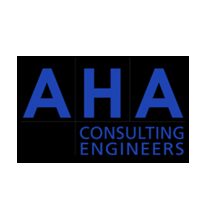
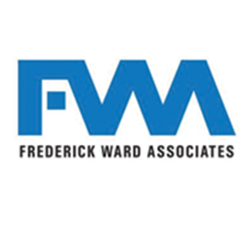
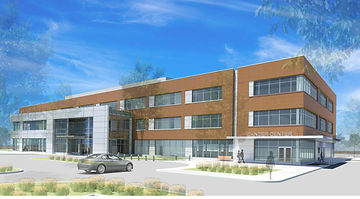
Architecture
Community Healthcare is currently under construction in the Mid-Atlantic region to serve as medical office and outpatient care center for the local community. The construction work has been bought out into two GMP packages one for the core and shell and one for tenant interiors. The primary tenant interiors package includes plans for a clinic, exam rooms, one operating suite, a LINAC Vault, ultrasound rooms, and physical therapy center.
International Building Code (IBC) 2012 | COMAR .05.02.02 Maryland Accessibility Code | National Electric Code (NEC) 2008 | International Fuel Gas Code 2012 | International Mechanical Code (IMC) 2012 | International Plumbing Code 2012 | National Fire Protection Association (NFPA) 101 | 2009 Life Safety Code 101 | State of Maryland Fire Prevention Code | COMAR 29.06.01 thru 29.06.14 | International Energy Conservation Code 2012
Codes Requirements
Zoning Requirements
Harford County Zoning Code Effective 12/22/2008 with Amendments through 5/21/2012 | B2 Community Business District; Medical Clinics | Maximum Building Height 3 Stories
Guidelines
ASHRAE 62.1 2007, FGI 2010
Building Enclosure
The front entrance of the building from the main parking lot is comprised of a curtain wall glazing system and composite metal panels. The Cancer Center entrance in the southwest corner of the building has a similar appearance with a glazed curtain system and composite metal panels. This mimicking of façade creates the two distinct entrances to the building. The first level surround the entire building is primarily this curtain wall and composite metal panel system. The second and third levels are brick veneer with windows and some composite metal panels for consistency of design. The details below show typical details for the curtain wall (A5), metal wall panel (B1), and brick veneer (C4).
Historical Requirements
No Requirement

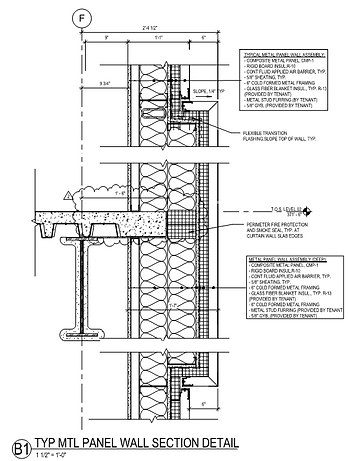
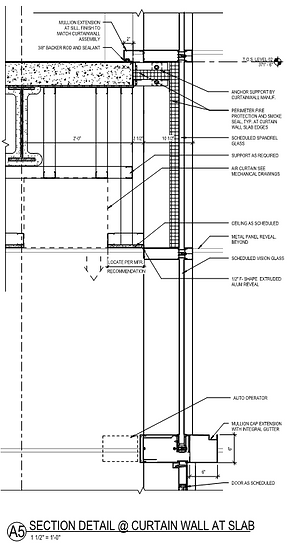
Roofing System
The roofing system consists of a built-up roofing system utilizing both consistent and tapered insulation for proper drainage and thermoplastic polyolefin (TPO) single-ply roofing membrane. The majority of the roof membrane is white TPO while the roof above the main entrance is a ballasted TPO, meaning that gravel or a small aggregate is placed on top. Also included on the roof above the main entrance is a skylight. Detail A4 (right) illustrates how this skylight ties into the roofing membrane. Much of the mechanical system is also located on the roof. To support this load, a concrete slab was poured for the equipment in the center of the roof along with larger steel members in area. Additional steel members were also added to frame out the opening for the mechanical shafts. There is also another opening on the north corner of the building's roof surrounded by ceramic tile. This opening is the quench vent for the MRI machine. Another feature of this roof includes a green roof assembly above the LINAC machine on the backside of the building.

Sustainbility Efforts
While LEED credits are not being tracked on this project, sustainbility was accounted for in the design. LED lighting and occupancy sensors were used in the electrical and lighting design. Additionally, the building utilizies a green roof above the LINAC machine. During construction, the waste and recycled material are being tracked.
Building Statistics Part II
Construction Means & Methods
Construction for this project was bought out in two packages: core and shell and tenant interiors. In order to be most time effective, the construction for both of packages occurred simultaneously when possible instead of phased construction. Additionally with such a large flat site, the logistics for this project are fairly simple and often allows for the most cost effective solutions and methods to be utilized. For this reason, a mobile crane was used primarily for the installation of the building structure that was easily driven offsite once the work was completed. The structural steel was placed from the south to the north with the main entrance last. Following the structural system, the façade is being placed by a combination of hydraulic and tube scaffolding along with boom lifts. This system was placed from the long west side to the north followed by the east and south elevations. Fortunately, with this large site, there is plenty of laydown area, which allows for most materials to be stored onsite and aids in preventing delays. The interiors are being completed by floor despite the fact that the building will not have phased occupancy.
Building Systems
Substructure & Superstructure
The building’s foundations are comprised of spread footings at column bases and stepped footing at concrete walls with a 5” slab on grade. In addition to the building foundations, a foundation and concrete vault had to be built for the Linear Accelerator Machine (LINAC) for the primary tenant. This room requires a minimum 4’ thick concrete walls and up to 7’-6” thick to prevent radiation from the machine from leaving the chamber. The LINAC structural plan is shown on the right. The building structure is structural steel frame with elevated concrete slabs on composite steel floor decking. The structural slabs are 2 ½” light weight concrete over 3” deep x 20 gage galvanized composite steel deck, for a total thickness of 5 ½” reinforced with 6x6-W2.1xW2.1 welded wire fabric. Typical beam sizes are W16x26, for spans between interior bays, or W18x35, for spans on exterior bays. These spans range from 28’6” to 36’. Girders are generally W24x68 on the second level and W24x55 on the third level.

Curtain Wall
The building has three glazing systems including curtain wall, storefront, and ribbon windows. The curtain wall system is incorporated into the main entrance along with decorative metal panels. The storefront windows are located on the first level where the curtain wall is not and some places on the second level on the front of the building. The ribbon windows then appear on the second and third levels. The figure below shows an elevation of these three systems on the front façade.


Electrical System
High voltage is provided by the local utility and comes into a transformer. From the transformer power is carried to the 4000 AMP main switchboard by way of eight sets of 4#500KCMIL wires providing 480/277V, 3PH, 4W power. Two transformers step down power from 480/277V to 208/120V to bring power to the first and second levels. There is also a distribution panel located on the third level for future buildout of that space. There is also a plan for a future generator to be added to the project in years to come.
Lighting Design
The community healthcare building utilizes several different lighting forms to accomplish its many usages. For more critical spaces or highly occupied spaced spacing, including equipment rooms and waiting rooms, LEDs lamps are used for their lifespan. Recessed and pendent LEDs are used in these spaces. Recessed LEDs are in equipment rooms and elsewhere, while pendent LEDs are tied into the interior design of public spaces. Additionally, there is a specific MRI rated LED downlight in the MRI room. Meanwhile, in less critical spaces, fluorescent lamps are used in all exam rooms. These fluorescents are typically 2’x2’ or 2’4’ recessed fluorescents. Many to most of the fixtures are on dimmers for occupant comfort.
Mechanical System
The mechanical system of this building is fairly simple. Three rooftop air handling units (AHU) deliver approximately 37K CFM per unit. Variable air volume terminals (VAV) are located throughout each floor to ensure occupant thermal comfort. Ensuring that there are different zones is especially important in this building since different rooms have varying purposes in the health and treatment of patients. Fan powered terminals are there to be sure to distribute air equally through large open spaces. Unit heaters can be found in spaces that are not continuously occupied for example stairwells and storage rooms.
Fire Protection
Due to the low overall square footage and low building height, wall partitions have at maximum only a 1-Hour Fire Rating. These 1-Hour Fire Rated Partitions are located around all means of egress including stairwells and elevator banks. While the fire protection and sprinkler systems are delegated design, per IBC 903, an automatic sprinkler system is required; wet-pipe sprinkler systems are specified for this project. Fire alarms, smoke detection, and portable fire extinguishers are all required systems as well. The standpipes, rated for 175-psig, will be located in the two exterior stairwells at the building’s edge and will need to be inspected by the local jurisdiction.
Transportation
Users of the Community Healthcare faculty can make their way through the different levels of the building by means of two elevators, three staircases, and one service elevator. Primarily the two elevators will be used by the visitors and patients of this healthcare faculty, while the remaining stairways will mostly be reserved for employee usage only. The service elevator allows for equipment and other maintenance items to be brought up to the second and third level without disrupting daily activities and usage. Additionally, the service elevator will need be utilized to fit out the remaining interiors on the two upper levels.

Telecommunications
The majority of the telecommunications for this faculty are centered on the separation of public and private spaces. The security for many of the spaces has to be limited to employees with clearance for the safety of the public. Not only do many of the rooms especially equipment rooms have card readers, but there are also fixed position cameras throughout the faculty. Another concern for this faculty is the possibility of intrusion. Therefore, there is a keypad for the instruction detection system along with a panic button on the nurses’ station in the case that the safety of the building’s staff and patients are under threat. This panic button will notify the local authorities to come immediately. Also for the safety of the patients, there are emergency station pull cords in the toilets and showers in case that a patient needs nurses’ assistance.